Berend van Wachem
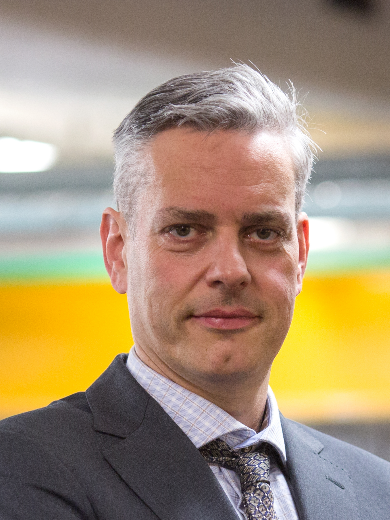
Prof. Berend van Wachem
Session: Mechanical and Thermal Preprocessing
Title: The Application of Discrete
Element Modelling in Gas-Solid
Processes
Berend van Wachem obtained his PhD in 2000 from Delft University of Technology on the modelling of gas-solid fluidized bed processes. After spending time in Sweden as a Lecturer, he joined the faculty of the Department of Mechanical Engineering at Imperial College London, UK, where he was appointed full Professor of Multiphase Flows in 2014. In 2017 he was appointed Chair of Mechanical Process Engineering, Faculty of Process and Systems Engineering, Otto-von-Guericke-Universität Magdeburg, Germany.
The main research areas of Berend van Wachem are Multiphase Flow, Particle Technology, Numerical Methods, Fluid-Structure Interaction and Computational Fluid Dynamics. The goal of his research is to develop a holistic research approach across the scales for understanding complex interactions between particles themselves and particles and flows and to disseminate this approach and its results to society and industry. This consists out of the development and application of theoretical, experimental, numerical and computational research. The funding for his research comes from Governmental funds (DFG, EPSRC), the European Union (EU), the AXA Research fund, Petrobras, Shell, Rolls-Royce and Astra Zeneca. Berend van Wachem is the author of 108 peer reviewed journal publications, 123 conference proceeding papers and has contributed chapters to 4 books.
The Application of Discrete Element Modelling in Gas-Solid Processes
The coupling of discrete element models (DEM) with computational fluid dynamics (CFD) constitutes a family of simulation tools to predict the behaviour of particles in flows, which are omnipresent in the process engineering. The coupling between DEM and CFD can occur at different scales and with different approximations. At the smallest scales, a coupling can be made with fully-resolved direct numerical simulation (DNS). This means that all the fluid length- and timescales are resolved and the interface of each of the particles with the fluid is resolved. Although this provides very accurate results, the computational cost is very high and this technique can typically only be used for academic cases. Alternatively, the fluid is resolved at a much larger scale than that of an individual particle, and closure models are required to account for the effect of the particles on the local fluid. This approach is commonly referred to "point-particle" simulations. The coupling of such simulations with DEM is a versatile approach and can be used to simulate millions of small particles.
In this talk, I will discuss these two approaches and give some details of each of them. I will also introduce a novel "point-particle" approach based on the filtering of the fluid governing equations, which leads to a much more accurate coupling of the behaviour of the fluid with the particles. During the talk, I will give a number of examples, including fluidized beds as well as separator devices, and illustrate the capability of coupled DEM and CFD frameworks. This includes predicting the effects of particle size, density and shape, as well as incorporate effects at the individual particle scale, such as comminution, adhesion and gas-solid chemical reactions. The predictive capability of such frameworks plays a crucial role in designing and improving processes involved with mechanical and thermal processing.